The last time President-elect Donald Trump used tariffs to wage the US-China trade war, it upended US ports. Suppliers rushed to frontload inventory ahead of implementation dates, straining infrastructure ill-equipped to handle the volume surge.
The COVID pandemic only accelerated the untangling of global supply chains.
Logistics firms say the lessons from those experiences and the changes implemented since may help cushion the blow if Trump makes good on promises to hike tariffs on US imports .
“What I think people learned was not to make huge volume rash decisions,” said Paul Brashier, vice president of global supply chain for ITS Logistics, referring to the 2018 trade war. “[There was] a lot of knowledge and infrastructure that was put in place to be able to handle situations like this that still exists so it mutes the overall effect when there are these changes in booking behavior.”
To be clear, some businesses are rushing to get ahead of any tariff hikes. At the country’s largest port, cargo volume was up 16% year on year in November, according to Port of Los Angeles director Gene Seroka, although he attributed much of that spike to geopolitical issues and a strong economy.
Read more: How do tariffs work, and who really pays them?
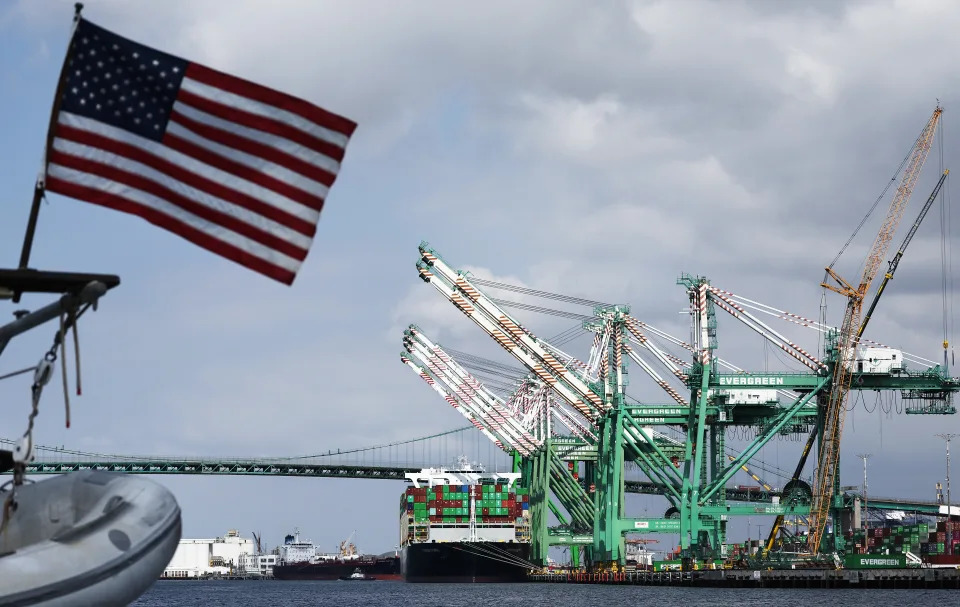
But as firms dust off their 2018 tariff playbooks, many are confronting a very different global trade landscape that is more diversified to withstand potential shocks.
For example, while China’s share of US imports amounted to 20% in 2017, today that share has declined to a 20-year low of 13.5%, according to research by Goldman Sachs. That shift has been especially pronounced in sectors like technology, where firms have increasingly distributed manufacturing outside of China to regional hubs like Southeast Asia and Mexico . Earlier this year, Mexico overtook China as America’s largest trading partner for the first time in decades.
Brashier has personally overseen the supply chain changes for ITS Logistics. Since 2018, the firm has opened new distribution facilities in Indianapolis, Reno, Nev., and Fort Worth, Texas. It expanded operations to 4 million square feet and added 3,500 additional transportation assets, including tractors, trailers, and chassis.
“There's a lot more infrastructure now that allows folks to ebb and flow and respond to what's going on with these kinds of headwinds that we see almost, it seems like, regularly,” he said. “I think that's the biggest thing that came out of 2018 and post-COVID.”
A perfect storm of shipping disruptions
Those reinforcements are sure to be tested as US ports brace for what could be the perfect storm.
In addition to the impact of potential tariff hikes, companies are bracing for disruptions that could stem from possible dockworker strikes at East Coast and Gulf Coast ports and the annual surge ahead of the Lunar New Year holiday in Asia.
Seroka said front-loading started in the third quarter of the year, but unlike in 2018, many businesses are taking a wait-and-see approach.
"We know there's a long way from the campaign trail to the implementation of public policy," he said. "What we need now is a clear line of sight as to where and when this policy may take shape."
US policy concerns only add to the long list of challenges shippers have had to navigate this year, particularly in response to disruptions in the Red Sea , where 12% of global trade used to pass through.
Companies have spent much of the year building inventories in the face of frequent delays and service reconfigurations, even as demand for container shipping remained strong.
Container volumes for November are projected to be up 14.4% year on year, according to Global Port Tracker . The Port of Los Angeles is on track to process 10 million container units for only the second time in its history, Seroka said.
Brashier has already begun mapping out contingency plans with importers for additional disruptions that are likely to emerge. That includes finding alternative points of entry into the US and monitoring the traffic flow. The ability to track freight the minute it hits water overseas gives imports a four- to six-week buffer, he said.
Brashier said other firms have begun seeking out additional warehouse space to store inventory.
Overseas suppliers are also weighing their options and negotiating lower prices for goods ahead of additional tariffs. They are concerned about losing business like they did in 2018.
One New Jersey-based home goods importer, who did not want his name used, said US firms are in a stronger position to "hit suppliers," particularly in China, since growth in the world’s second-largest economy has stagnated. He has no plans to reroute his supply chain, even if it means passing down higher costs to consumers.
“There [are] certain commodities that the infrastructure of China cannot be beat on, whether it's the raw material, access to ports, access to ships, access to transportation, access to a labor force,” he said. “We're not selling products at a loss. We're a for-profit entity.”